Retrofits for Engines in the Oil and Gas Industry
Reduce Fuel Consumption with Cat's Dynamic Gas Blending Technology
Efficiency improvements and cost savings are key challenges in the oil and gas industry. With our Dynamic Gas Blending (DGB) technology, we offer a powerful retrofit solution that enhances the efficiency of your engines and reduces operating costs – without compromising performance or reliability. By converting to Dynamic Gas Blending, you can significantly save on fuel costs by replacing expensive diesel with more affordable gas. The system adapts flexibly to load demands, allowing for maximum substitution, while the lifespan and service intervals of your engines remain unchanged.
Available for you 24/7
Germany
International
Key benefits for your organization
Cost Reduction
In the oil and gas industry, large amounts of diesel are required, especially for the operation of drilling rigs, generators, and pumps. DGB enables the partial substitution of diesel with more affordable gas, resulting in significant fuel cost savings.
Flexibility
The engine can operate with pure diesel or a blend of diesel and gas. The system dynamically adjusts the gas/diesel mixture ratio, depending on the availability of gas and the operating conditions of the engine.
Emission Reduction
The use of gas reduces CO₂ emissions as well as other harmful emissions such as nitrogen oxides (NOx) and particulates, compared to pure diesel operation.
Easy Integration
DGB systems typically do not require extensive modifications to the existing diesel engine, making the implementation cost-efficient and less complex. The engine retains the ability to operate fully on diesel in case gas is unavailable.
Zeppelin Power Systems services for Oil & Gas
The Dual-Fuel Engine Solution from Cat for Your Oil and Gas Drilling Application
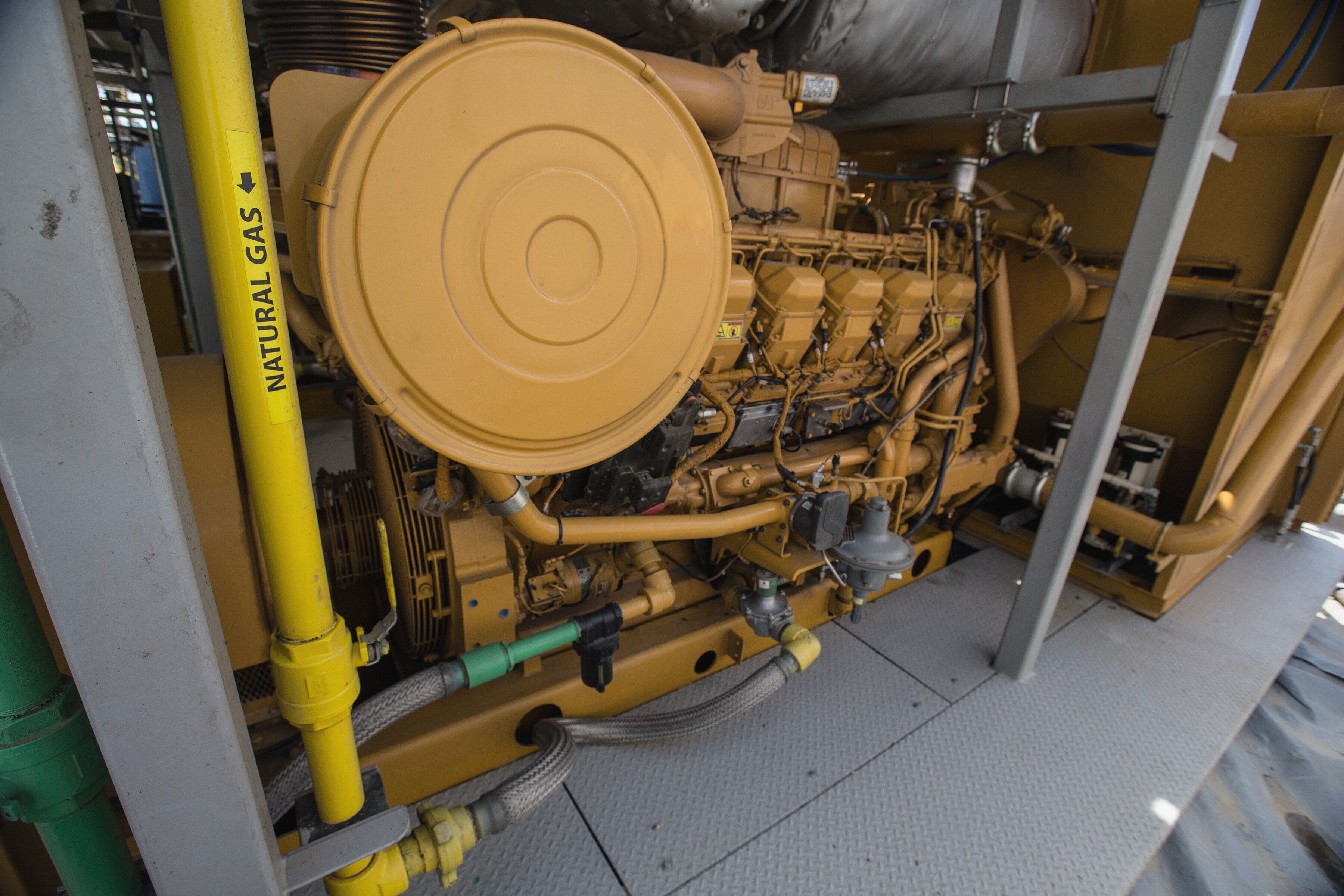
Oil and gas drilling rigs are often located in remote areas where the supply of diesel is costly and logistically challenging. As a result, Dynamic Gas Blending (DGB) is frequently used in the oil and gas industry. DGB offers the flexibility to use gas or locally available associated gas without having to forgo diesel as the primary energy source. We provide solutions that allow you to easily retrofit your gas engines.
Substitution of Diesel with Gas
Dynamic Gas Blending is a technology that allows diesel engines to run partially on gas, optimizing fuel consumption by flexibly blending gas with diesel. It automatically adjusts the mixture ratio based on operating conditions.
With Dynamic Gas Blending, you achieve maximum substitution while continuing to benefit from the usual service intervals – without compromising the performance of your diesel engine and with smooth transition behavior.
Customized Fuel Blending Systems
We offer customized fuel blending systems tailored to your specific requirements. The installation of the DGB system includes adjustments to the engine ECU, wiring harness, pressure sensors, and intake pipes to optimally control and monitor the fuel mixture. Additionally, the generator wiring and control systems are adjusted to ensure seamless integration. After installation, the DGB engine automatically adapts to the fuel quality without the need for on-site calibration.
Would you like to receive advice and more information?
What adjustments are necessary for the DGB retrofit?
The installation of a Dynamic Gas Blending (DGB) system affects several systems of the engine and power generation unit. Zeppelin Power Systems supports the entire process, from initial consultation to detailed assistance and the implementation of all required measures – ensuring smooth and safe integration of the system.
Key components affected by the retrofit include the Engine ECU (Electronic Control Unit), which is responsible for controlling and regulating the engine. It must be adjusted to efficiently manage the dynamic blend of diesel and gas.
The engine wiring harness, which controls all electrical connections in the engine, also needs to be modified to support the new control requirements of the DGB system. Additionally, engine pressure sensors are involved, which monitor system pressure and send data to the ECU, ensuring precise fuel mixing.
The intake air piping and air filter brackets play a crucial role in supplying the correct amount of fresh air necessary for the combustion process. Changes to these systems are required to ensure that the air supply is aligned with the modified fuel mix. If a pre-cleaner is used, its brackets should also be checked and adjusted, if necessary, to optimize the interaction with the air supply and the gas-diesel blend.
On the power generation side, the installation of the DGB system also affects the generator wiring and generator control. These systems must be adjusted to efficiently control electrical output and synchronize the generator’s behavior with dynamic load demands driven by the diesel-gas mixture.
Overall, implementing a DGB system requires adjustments to various components to ensure seamless integration and optimal performance.
Zeppelin Power Systems services for Rail
Additional services at a glance
Show all Services for RailLooking for support? We are happy to help.
Zeppelin Power Systems Solutions for Oil & Gas
From Planning to Implementation: Your Drilling Projects from a Single Source
Show all Solutions for Oil & GasZeppelin Power Systems Resources for Rail
Brochures and certificates for Rail available for download
Show all Resources for Rail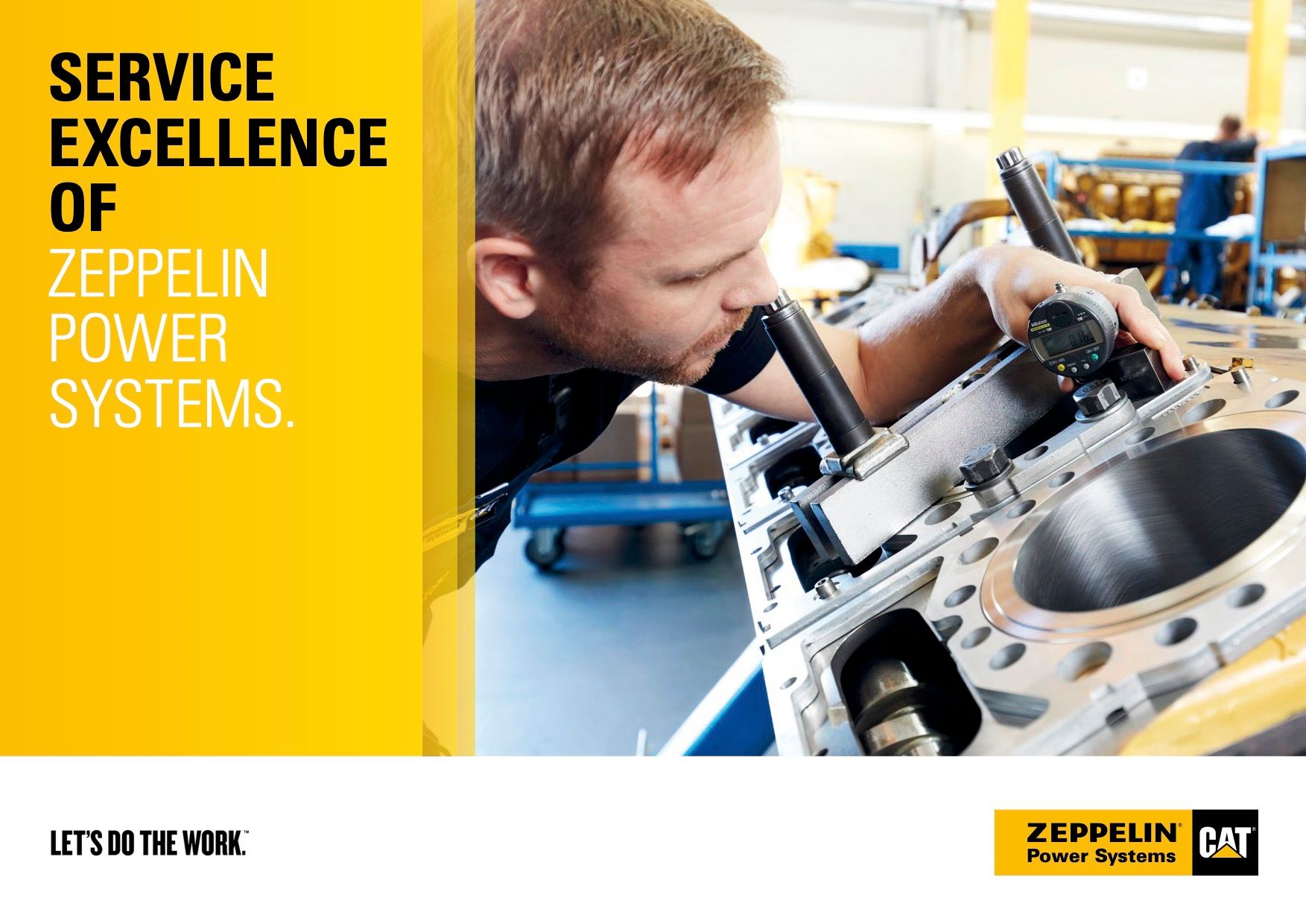
Upgrades & Retrofits for Rail Systems | Zeppelin Power Systems-You can find more information about our services in the brochure
You can find more information about our services in the brochure
Zeppelin Power Systems Portfolio
Explore more from the Zeppelin Power Systems portfolio
Power & Heat
Rail
© 2025 Zeppelin Power Systems GmbH